5 Essential Factors To Your Blast Chiller Design For Ultimate Efficiency
Designing an efficient blast chiller system involves more than lowering temperatures and increase air flow. By strategically planning around these five essential factors, you can boost energy efficiency and ensure quality product.
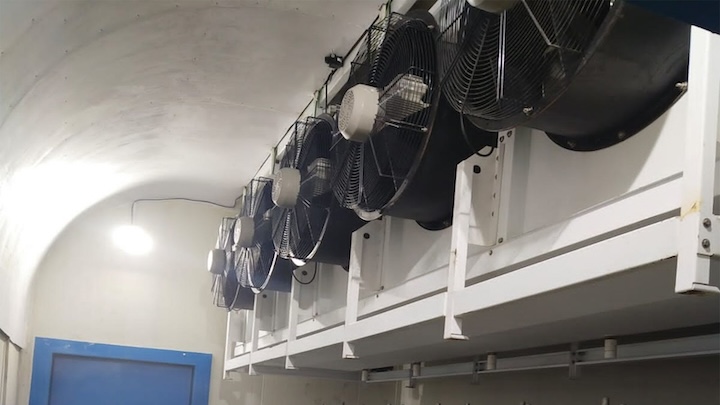
Read More